The Fletcher Water collective is the combination of our industry-leading capability in the water sector, through all of our business units.
The majority of our work in this sector is delivered by Brian Perry Civil, which has the people and plant to drive industry change in project delivery through innovation, early involvement, and safer delivery methods.

Brian Perry Civil is constructing the Whakawhirinaki Pipe Bridge for Wellington Water Limited – replacing the large diameter bulk water pipeline across the Te Awa Kairangi / Hutt River in Upper Hutt.
Brian Perry Civil is constructing the Whakawhirinaki Pipe Bridge for Wellington Water Limited – replacing the large diameter bulk water pipeline across the Te Awa Kairangi / Hutt River in Upper Hutt. The bridge, which will also have walking and cycleways, was gifted the name Whakawhirinaki by local iwi at a dawn ceremony.
This is one of the region’s most critical water supply pipelines for the bulk water supply network, supplying all the water to Porirua City and North Wellington. In its current alignment it is seismically vulnerable, difficult to maintain, and severely affected by corrosion.
The works include 1000m of new 1m diameter steel pipe across the river and through the Manor Park golf course. The new seismically resilient three-span pipe bridge across the river consists of a 100m network arch at the central span and steel trusses at the end spans.
This project, which will be completed in 2025, demonstrates BPC’s innovative, outside-the-box thinking to deliver value for clients. Through our ECI involvement, BPC and our project partners proposed an alternative design that drastically reduced the overall weight of the structure and seismic demand. This delivered a significant cost saving for the client and also reduced the carbon output by 1,914t.
At the karakia and naming ceremony, Taranaki Whanui Chair Kura Moeahu said Whakawhirinaki means ‘to lean against something, trust in something, depend on or rely on’. “Whirinaki is also the original name of the region,” Kura said, “so by naming this bridge Whakawhirinaki we are saying we trust in it and rely on it given the huge responsibility it has to carry our region’s water through Hutt Valley and Waiwhetu to its final destination.”
Client | Wellington Water Limited (WWL) |
---|---|
Budget | $58 million |
Completed | Under construction |





The Snells Beach Wastewater Treatment Plant, being delivered under the Watercare Enterprise Model (WEM), displays Brian Perry Civil's capabilities in delivering complex and vital infrastructure projec...
The Snells Beach Wastewater Treatment Plant, being delivered under the Watercare Enterprise Model (WEM), displays Brian Perry Civil's capabilities in delivering complex and vital infrastructure projects. This job will bring a new, modern, and efficient wastewater treatment plant to the Warkworth and Snells-Algies communities. Designed to cater to population growth over the next 35 years, the plant will ensure the highest standards of wastewater treatment while safeguarding the local environment.
By safely discharging treated water through the new outfall off Martins Bay, the Snells Beach Wastewater Treatment Plant will contribute to a significant improvement in the local ecosystem. The project's success will be marked by the decommissioning of the existing plant, bringing an end to its discharges into the Mahurangi River and harbour.
Construction commenced in early 2022. The project presents various challenges that demand a highly collaborative approach. Brian Perry Civil, alongside Watercare, consultants, and suppliers, is navigating the project's complexities to ensure its timely and successful completion.
Client | Watercare Services Ltd |
---|---|
Completed | Under construction |




Constructed by Brian Perry Civil, this 52m long Network Arch Bridge carries a new seismic resilient Kurimoto pipe over Te Awa Kairangi (Hutt River) in the Kaitoke Regional Park. The pipe bridge conveys water from the Hutt River Kaitoke intake to the Te Marua storage lakes, ensuring the safe supply of drinking water for the Wellington region.
A lot of preparation work was required before the new bridge could be installed in place. 900m3 of rock and vegetation was cleared from the northern slope and 400m3 of rock and vegetation were cleared from the southern slope of the valley to prepare for the installation of horizontal anchors to the rock face. This challenging work was done by abseilers supported with a small crawler crane. Over 200 horizontal rock anchors were installed, each drilled 6m into the rock face for earthquake stability and resilience.
Twenty vertical rock anchors were installed to widen the access road for larger machinery to access the site to both construct the new bridge and demolish the old bridge.
Each bridge abutment is made of six reinforced concrete piles embedded in the rock, with a capping beam tying them together. The bridge (superstructure) lies on bearings and a concrete slab, allowing sliding motion in severe seismic events. The web forge bridge walkway will have railings at two levels and a sliding joint at the abutments to connect to the northern and southern walkway ramps.
BPC installed a Favco M860D luffing tower crane for the works, which is the largest tower crane owned in New Zealand. With a 22m tower and 64m luffing boom it has the capacity to lift 11T at 62.5m radius or 32t at 32m radius. Its work at Kaitoke includes lifting a 10t piling rig at 60m radius to the other side of the river on temporary staging to perform the works, installing the 30t bridge steelwork, and removing the old concrete bridge sections during demolition.
Client | Wellington Water Limited |
---|---|
Budget | $32 million |
Completed | July 2024 |

Situated in the heart of Wellington, this intricate project involves the construction of the new pump station and connection to the existing wastewater network in Dixon Street and Taranaki Street, red...
Situated in the heart of Wellington, this intricate project involves the construction of the new pump station and connection to the existing wastewater network in Dixon Street and Taranaki Street, redirecting flows into the new pump station and then providing an outlet connection to the future Taranaki Street rising main.
The pump station is 10.88m external diameter, 8.66m internal diameter, with a floor level approximately 8.5m below ground. To construct this, we installed 42 900mm diameter secant piles 19m below ground level to form the new pump station’s superstructure.
Instead of the standard polystyrene blocks that would typically have been used for a guidewall, we opted for an environmentally friendly cardboard design that proved both environmentally friendly and cost-effective.
The project is required to address the existing undersized and aging wastewater network issues, in particular reducing pressure on the existing network, accommodating growth and providing resilience for critical wastewater infrastructure.
Client | Wellington Water Limited |
---|---|
Budget | $7 million |
Completed | March 2024 |




The disused Papakura Water Treatment Plant was reinstated as part of Watercare’s drought management plan. Built over two stages, the project plays a vital role in boosting water supply resilience to Auckland.
In Stage One we constructed a temporary treatment plant, taking water from the Hays Creek Dam, and a pipeline to connect it to the network. We also constructed a 9m high bored pile retaining wall and all associated earthworks to create a platform to accommodate the new plant.
Stage Two involved construction of a permanent treatment plant providing 12 ML/d of Aa-graded drinking water to Auckland residents. This included 4 clarifiers, membrane train, UV treatment and 4 BAC filters. We also completed difficult structural repairs to existing 70-year-old reservoirs and new interconnecting and outlet pipework. This was undertaken in an extremely congested site with minimal laydown area so required careful coordination between the multidisciplinary team.
The project demonstrated BPC’s technical excellence, collaboration, innovation, and exceptional Health and Safety, bringing tangible relief to the Auckland community.
Client | Watercare Services Ltd |
---|---|
Completed | July 2023 |




When contacted by Stantec in January 2021 to help develop a solution for the Porirua Wastewater Treatment Plant, the team at Brian Perry Civil knew they could help.
When contacted by Stantec in January 2021 to help develop a solution for the Porirua Wastewater Treatment Plant, the team at Brian Perry Civil knew they could help. BPC was engaged through Early Contractor Involvement for our client Wellington Water through their CAPEX panel. The team reviewed the permanent works design concepts and flagged the potential requirement for expensive and extensive temporary overpumping. BPC proposed the novel idea and a different approach to the temporary works required. By establishing a bypass of the treatment plant inlet works, supported by a semi-permanent step screen, a viable solution was developed. This solution generated a 16% cost saving, a significant achievement for Wellington Water, Porirua City Council, and their stakeholders.
Works commenced onsite in November 2021. The project was delivered efficiently and the team adapted to meet design changes and the requirements of working in an operational treatment plant. Working collaboratively with plant operator Veolia, the BPC team maintained open communication while also assisting with small repairs around the plant. Works were completed in April 2023.
Since the bypass step screen was installed there have been no untreated discharges into Tītahi Bay, as the bypass system was sized to the new hydraulic flow requirement.
Client | Wellington Water Limited |
---|---|
Completed | April 2023 |
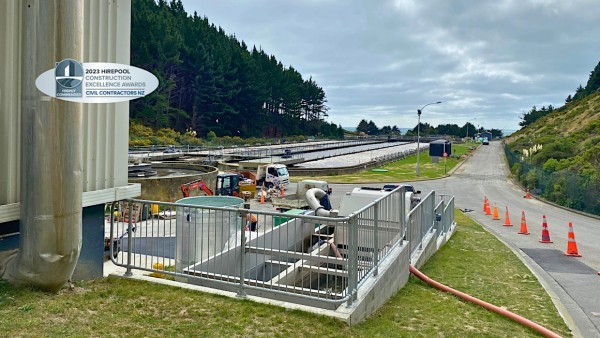

BPC combined pace, digital smarts, and deft collaboration alongside the client, Watercare Services Limited, equipment supplier, Veolia, and lead designer, Beca, to deliver a critical piece of wastewat...
BPC combined pace, digital smarts, and deft collaboration alongside the client, Watercare Services Limited, equipment supplier, Veolia, and lead designer, Beca, to deliver a critical piece of wastewater infrastructure that will see Watercare continue to meet the growing environmental and sanitation needs of Auckland’s northwest.
In November 2021, Watercare instigated the fast-tracked Helensville Wastewater Treatment Plant Upgrade to re-optimise the treatment performance of the plant. In less than a month, there was a committed programme to procure, design, consent, and construct the project within a year, with an additional 3 months to commission. A year later, with all major equipment installed, the commissioning team successfully brought the upgraded facility online.
Main construction activity took place on an earth dam with significant restrictive loading limits, dictating construction and installation methodology. This included ground stabilisation, structural works, pavements, drainage, M&E, and commissioning – all while the existing plant remained operational.
To improve the Plant’s performance and achieve compliance, a new Membrane Aerated Biofilm Reactor was introduced to the treatment process, installed upstream of the existing Ultra Filtration process.
Client | Watercare Services Ltd |
---|---|
Completed | February 2023 |
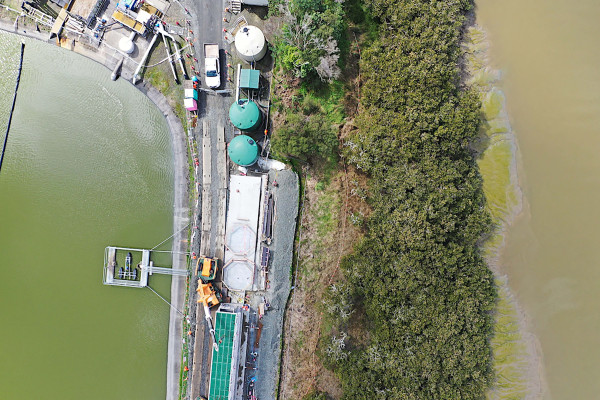

Auckland’s Northern Interceptor is a new pipeline that redirects wastewater from the Hobsonville Pump Station to the Rosedale Wastewater Treatment Plant. Brian Perry Civil delivered a separable portion of roughly 2.5km of watermain and 1.5km of sewer rising main. The accelerated timeline meant the design was incomplete when construction started. The alignment changed soon after tender. Installing a 1200 dia. CLS pipe and numerous service ducts through a tunnel underneath SH16, down a 9m deep shaft, was a huge challenge – one that we self-performed safely and successfully, with the carrier pipe then installed by a subcontractor.
Most of the watermain was constructed via open trenching, within the public road reserve, with bored tunnelling for the section under the SH18 motorway. Key to the successful delivery was our ability to work collaboratively in a wider multidisciplinary team, provide constructability expertise, and self-perform large volumes of pipeline installation and associated complex civil works alongside and underneath SH18.
Client | Watercare Services Limited |
---|---|
Budget | $25m separable portion |
Completed | July 2022 |







Two major stormwater culverts were constructed under a West Auckland arterial road to mitigate the risk of a substantial washout after a major rain event.
Two major stormwater culverts were constructed under a West Auckland arterial road to mitigate the risk of a substantial washout after a major rain event.
The multidisciplinary scope of works included: constructing two single span structures with precast concrete roof slabs; major road realignment and traffic management; installing over 200 bored piles up to 25m deep; protecting major regional above and below-ground services, including the Huia 2 watermain feeding the Waitakere dam supply into the greater Auckland network the IP20 gas main feeding gas to West Auckland and relocations of smaller local services; potable water, sewer, stormwater, power, and gas lines; and upgrading and stabilising the upstream and downstream embankments and streambed.
Early Contractor Involvement was key to the project’s success. BPC and the various asset owners workshopped the constraints around each element and optioneered solutions and potential construction methods.
The project delivered a future-proofed asset for Auckland Transport and a more resilient stormwater and transportation network for West Auckland.
Client | Auckland Transport |
---|---|
Budget | $28 million |
Completed | May 2022 |






Brian Perry Civil delivered the upgrade of two pump station’s inlet structures over one construction season.
Brian Perry Civil delivered the upgrade of two pump station’s inlet structures over one construction season. The upgrades improve equipment access to screens for weed clearance and health and safety upgrades.
The project involved a construction of a range of items including:
- Design and construction of a temporary cofferdam
- Dewatering and groundwater management
- Driven timber piles and reinforced pile caps
- Supply and installation of new precast box culverts and L-sections.
Innovative thinking was key to the success of the project. Examples of innovation included clever use of excavators to help access difficult to reach areas and assisting our suppliers through the independent procurement of steel.
By every success metric in the industry, the Mill Road pump stations achieved them zero harm, on time, on budget, and to quality, environmental and other project requirements. Upskilling our team was another great outcome, where they all had the opportunity to step up and gain experience that will progress them in their career development.
Client | Waikato Regional Council |
---|---|
Budget | $1.5 million |
Completed | March 2022 |




Design and construction of a new water treatment plant on a greenfield site.
Design and construction of a new water treatment plant on a greenfield site. The project was designed to resolve the increasing water supply demand in Te Awamutu and the Waipa district and to future proof water supply against the projected growth in the area.
The plant can produce a flow of 12,000m3/day net treated water, readily expandable up to 16,000m3/day.
The project included:
- A water treatment building to house membranes, UV, chlorine gas, peroxide, chemical dosing system, electrical & control room, operational offices, kitchen, shower, and bathroom facilities.
- A treatment process to comply with the treated water quality requirements inclusive of all chemical dosing, pre-treatment, backwash, instrumentation, services, and compressed air.
- Above and below ground civil works, landscaping, planting, roading and water networks.
- Reservoir and storage Tanks – 1.5ML treated water storage tank and a 275m³ flocculation tank.
- Two waste sludge ponds
- Inface connections with the existing water treatment plant, potable water network, and utility services.
Client | Waipa District Council |
---|---|
Budget | $17.9 million |
Completed | October 2021 |





Responding to what was then the most extreme drought in the Auckland region in modern times, Watercare activated an emergency drought response project to deliver an additional 50 million litres of treated water per day from the Waikato River. The entrant organisations collectively designed, consented, procured, constructed and commissioned a new water treatment plant in 12 months, a process that would normally take four years.
The complex and rapid nature of the programme presented unique challenges. These were addressed through innovative digital engineering that contributed to the success of the project: completion on time and under budget, without compromising environmental outcomes. An additional water source for the region was required to maintain water security and reduce the need for further water restrictions.
Fletcher Construction and Brian Perry Civil employed innovative digital techniques to manage bulk earthworks and produce erosion and sediment control plans, where a lack of accurate and up-to-date topographical and aerial imagery existed for the site. Topographical survey data and digital tools were used to design sediment retention ponds that were accurately constructed with GPS-enabled excavators. 3D as-built models of the erosion control devices were used to confirm compliance with design criteria and sediment control guidelines.
Client | Watercare Services Limited |
---|---|
Budget | $89 million |
Completed | June 2021 |



BPC was engaged through the Watercare Enterprise Model to undertake Early Contractor Involvement (ECI) and construction works for the Chlorine Emergency Gas Scrubber at Watercare’s Ardmore Water Treat...
BPC was engaged through the Watercare Enterprise Model to undertake Early Contractor Involvement (ECI) and construction works for the Chlorine Emergency Gas Scrubber at Watercare’s Ardmore Water Treatment Plant, to provide protection from the hazards of having a large volume of chlorine gas stored onsite.
The ECI focused on developing options to increase installation productivity to improve operational health and safety, and reduce carbon and costs. A 40% carbon reduction was identified by altering the proposed construction method. It reduced overall manhours, raw materials cost, and the number of plant shutdowns required.
BPC was engaged post-ECI to provide a detailed construction cost and programme that was accepted, with procurement and setup starting immediately. Having completed two previous back-to-back contracts on the site – Ardmore Water Treatment Plant UV Upgrade and Ardmore Sludge Handling Upgrade – BPC was easily able to deliver.
The works included: structural upgrades for the scrubber ducting; HVAC upgrades; electrical and process upgrades; and the procurement on long lead scrubber vessel and media. The project was delivered on budget and with an accelerated programme to meet the client’s requirements.
Client | Watercare Services Ltd |
---|---|
Budget | $1.97 million |
Completed | April 2021 |
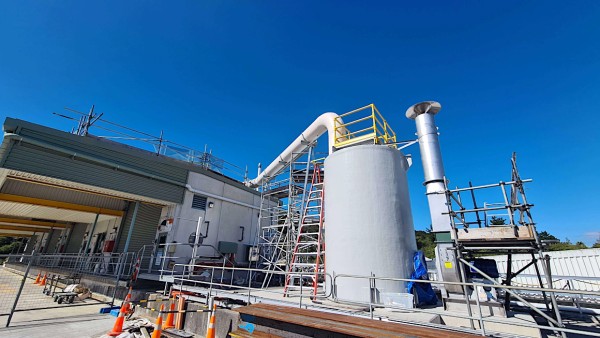

The Hay’s Creek Pipeline project included installing a new 600mm cement lined steel pipeline along Hunua Road to carry an extra 6 million litres per day of Aa-graded drinking water across the network ...
The Hay’s Creek Pipeline project included installing a new 600mm cement lined steel pipeline along Hunua Road to carry an extra 6 million litres per day of Aa-graded drinking water across the network from the recommissioned Papakura Water Treatment Plant (also delivered by BPC). The project was completed LTI-free while creating positive relationships within the community.
With the project becoming a priority as part of Watercare’s emergency response to Auckland’s drought, there was a tight timeframe to pull a team together, properly understand site constraints, obtain necessary approvals, and form a sound methodology.
The project was delivered two weeks early – impressive considering the unforeseen service clashes encountered, including a 40m asbestos pipe running obliquely to the new pipe alignment, a service relation scope being extended, and an additional scope of installing four new manholes being awarded after pavement preparation work had been completed.
Client | Watercare Services Ltd |
---|---|
Budget | $6 million |
Completed | December 2020 |
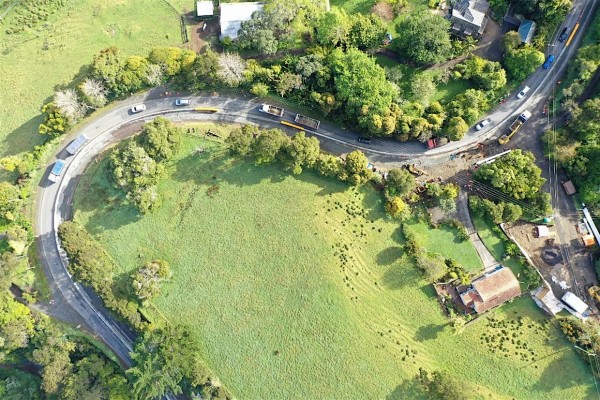

Watercare improved Auckland’s water capacity in response to the long-lasting drought, increasing water capacity to 175 million litres per day in 2020.
Watercare improved Auckland’s water capacity in response to the long-lasting drought, increasing water capacity to 175 million litres per day in 2020. With this increase in volume, an upgrade of the Chemical and Electrical Systems of the existing plant was required. BPC was contracted to inform design through ECI, working closely with Watercare and BECA to achieve a design that was efficient and economic to build.
The CSEU project typified multidisciplinary civil construction, in line with many others that BPC have delivered for the water industry. This included significant scopes for foundations, concrete construction, structural steel, pipelines and utility services, mechanical installations, electrical and control systems upgrade and commissioning. BPC self-performed the majority of the work, including all electrical works. The brownfields nature of the project meant that the team were constantly interfacing with existing live processes that were critical to maintain plant operation.
Being on the banks of the Waikato River and operating near areas of historical and cultural significance the project team ensured positive engagement with mana whenua. The project hosted a special toolbox with representatives from Te Taniwha o Waikato and kaumātua Marti Ngataki and George Katipa, who shared the history of the area and discussed its many significant features.
Client | Watercare Services Ltd. |
---|---|
Completed | 2020 |
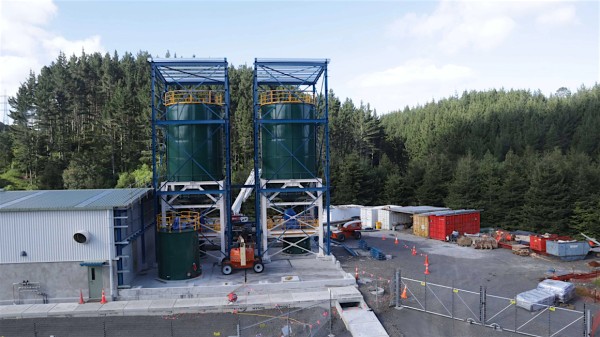

January 2020 saw two critical sludge pipes lose pressure and fail, forcing Wellington Water (WWL) to transport sludge by truck 24/7.
January 2020 saw two critical sludge pipes lose pressure and fail, forcing Wellington Water (WWL) to transport sludge by truck 24/7. Investigations revealed a pipe burst 250m inside the Mt Albert tunnel. This was a gravity pipe carrying wastewater to the city’s water treatment plant, buried deep under the city’s town belt.
Built to last at least 80 years, WWL did not expect one, let alone two, sludge lines to fail with an earthquake the probable cause. Both ruptured pipes were encased in a concrete surround within a 1.85km long tunnel running from Island Bay to Lyall Bay. The tunnel had only one access shaft and shutting down the feeding pump station for longer than an hour was impossible. Further complicating the situation was the fact that repairs needed to be made remotely.
WWL engaged Brian Perry Civil and Stantec to design a solution. The project team concluded a full pipeline liner was the most appropriate repair method. Two 1.8km liners were procured from Amex Samivar in Germany, the longest it had ever produced. Working seven days a week during the COVID-19 level 4 lockdown, BPC’s crew ensured the site was ready for the liners’ arrival and arranged for five Amex technicians to come to New Zealand to assist with the installation.
On May 21, the first pipeline was switched back on with the second pipeline repaired in June. BPC then moved on to the second stage of the project to repair damaged sections of concrete 250m from the tunnel access point. Communication and ventilation systems were installed to provide safe access to the challenging confined space for this work. A comprehensive community engagement programme also saw the project team working with closely with residents to address their needs and concerns.
Client | Wellington Water Limited (WWL) |
---|---|
Budget | $7.6 million |
Completed | December 2020 |
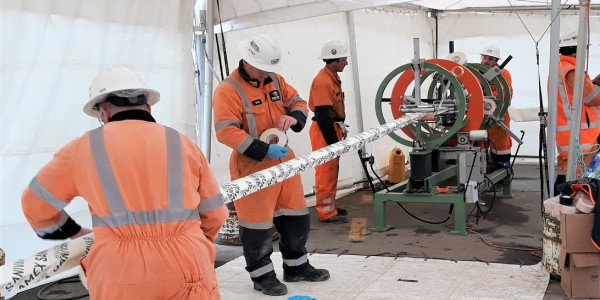

BPC upgraded the Ardmore Water Treatment Plant to enhance its reliability and sludge handling capacity.
BPC upgraded the Ardmore Water Treatment Plant to enhance its reliability and sludge handling capacity. As head contractor, BPC was required to replace two existing sludge presses in the operational water treatment plant with a new client-supplied centrifuge and sludge press to match existing and associated equipment and pipework.
The project included removing two existing presses, installing a centrifuge and one new press, two new switch rooms, and one new electrical building. The work included an associated timber retaining wall and electrical systems to provide dual redundant electrical supplies from the HV ring main to the new equipment.
The project required designing and constructing a temporary support frame to enable the removal of the existing presses, as well as the removal and reinstatement of the existing building façade to facilitate the installation of the new presses.
Client | Watercare Services Ltd |
---|---|
Budget | $5 million |
Completed | August 2020 |
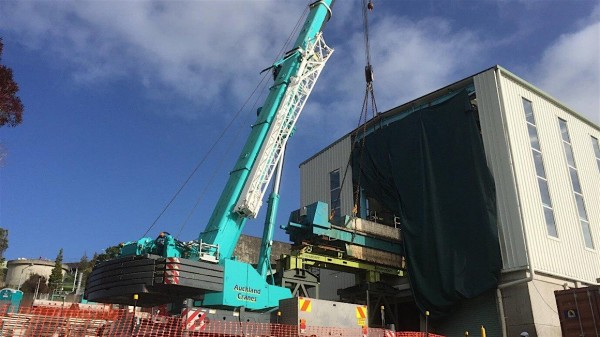

Commissioned to increase the resilience of the Ardmore Water Treatment Plant after a major storm event in 2017, this project involved retrofitting ultraviolet treatment to the filtered water stream to...
Commissioned to increase the resilience of the Ardmore Water Treatment Plant after a major storm event in 2017, this project involved retrofitting ultraviolet treatment to the filtered water stream to provide a second protozoa barrier.
The project included: constructing a new UV inlet / overflow chamber; installing a new overflow pipe; a 3m excavation of the UV reactor room and underpinning the existing water tank walls, undertaken while the Plant remained operational; procuring and installing three of New Zealand’s largest DN1200 K143 UV reactors plus components, pipework, and ancillary equipment to operate the UV reactors; modifying the mixing tank weir to achieve the specified flow targets; electrical, control, and instrumentation works; and integrating these works into the existing WTP.
Given Ardmore’s importance in the wider network, Watercare sought to improve capability quickly, engaging BPC in a direct appointment ECI to develop, design, and construct an efficient and practical solution. It had to be retrofitted within the existing plant, without compromising throughput.
Client | Watercare Services Ltd |
---|---|
Budget | $12 million |
Completed | August 2020 |


BPC was contracted for Phase 1 of the East Side Villages Wastewater project, and subsequently awarded Phases 2, 4, and 5.
BPC was contracted for Phase 1 of the East Side Villages Wastewater project, and subsequently awarded Phases 2, 4, and 5.
Phase 1 involved the rehabilitation of Clarigester No. 1, upgrades to the influent pump station, and chlorine contact chamber piping modifications at the Utulei Wastewater Treatment Plant.
Phases 2 and 4 involved the construction of the 20” Ø sewer force rising main from Malaloa to Utulei, and the construction of the 12” Ø sewer force main from Malaloa to Leloaloa. The project was split into two packages (2 and 4) which were awarded as a combined package.
Phase 5 involved three new sewerage lift stations; force mains and lateral sewers; service connections to existing facilities and decommissioning of existing septic tanks and cesspits; and new sewer manholes, concrete works, metal works, and electrical work.
Highlights of the project included successfully excavating around an abundance of existing services, both known and unknown, and the successful completion of the Horizontal Directional Drill under the river. Significant effort was put into training local employees in the specifications and skills required, leading to a more capable and resilient workforce.
Client | American Samoa Power Authority |
---|---|
Budget | $19.5 million |
Completed | January 2020 |
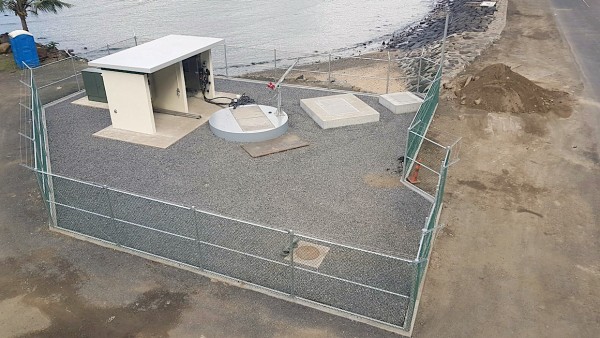

Wellington Water Ltd (WWL) engaged GHD consulting engineers to design a combined drywell/wetwell pump station and rising main pipeline. This involved constructing a new 6.5-metre diameter, 7-metre deep underground pumping station, including mechanical fit-out, and 175 metres of new rising main on a contaminated site. Brian Perry Civil provided an innovative solution based on the segmental precast caisson system.
The project involved working from the top down with a pre-made segmented ‘jigsaw’ of concrete panels—the first time such an approach is believed to have been completed in New Zealand. This approach meant there was no requirement for large scale temporary works (shoring). That's because the caisson method uses the absolute minimum footprint of the excavation, without over-digging for working space, reducing the volume of material to be excavated. Another benefit was minimising the volume of contaminated material, from the high levels of petro-carbon contaminants in the groundwater, that had to be removed.
The central city site created many challenges that the segmental caisson system helped overcome. This system is constructed in one metre increments at ground level and then pushed into the ground using hydraulic jacks. With no vibration effects from this method, the danger to adjacent structures (including a three-storey unreinforced masonry structure) was overcome. The system also helped overcome the risk of excessive noise for residents and businesses. A vulnerable tree within one metre of the site was saved by moving the location of the pump station by 300mm. Careful planning also ensured two lighting columns within one metre of the new structure were able to be retained during the project.
Another challenge came from discovering significant differences from the records provided, including much deeper banks of cable than had been anticipated in the original design. A directional drilled solution that minimised risk to underground services and traffic management was employed.
Using innovative solutions and out-of-the-box thinking turned difficult challenges into a real success story on this project. Brian Perry Civil’s innovation was recognised with a Civil Contractors New Zealand’s Branch Construction Award in May 2019.
Client | Wellington Water |
---|---|
Budget | $2.46 million |
Completed | May 2019 |






Brian Perry Civil delivered a new, state of the art Thickening and Dewatering Plant for Tauranga City Council at the operational Te Maunga Wastewater Treatment Plant.
Brian Perry Civil delivered a new, state of the art Thickening and Dewatering Plant for Tauranga City Council at the operational Te Maunga Wastewater Treatment Plant.
The new facility involved the construction of:
- a two-storey architectural building,
- ground improvements,
- sludge load out facility
- two 16m diameter concrete PFT tanks,
- deep pump station installations,
- two 10,000L storage tanks,
- mechanical and electrical installations, and
- new access roads.
Working in an operational wastewater plant environment where ground conditions were poor and prone to liquefaction required careful planning to ensure we delivered the project to meet quality and programme requirements.
The site was highly-constrained, as was the programme, requiring constant coordination and problem solving to ensure the new plant was delivered safely to Tauranga City Council’s requirements whilst maintaining the existing plant operation. All subcontractors took part in a weekly coordination meeting and a logistics board was developed to ensure deliveries did not clash.
Our team was solutions-focused and innovated in their adaptation to unforeseen ground conditions by changing the ground improvement technique. The method was changed from insitu mass stabilisation to deep soil mixing piles. To achieve the original performance specification, we constructed 490 600mm diameter piles and overlapped them to form a continuous grout block.
Client | Tauranga City Council |
---|---|
Budget | $15 million |
Completed | April 2019 |





With an ageing stormwater culvert in the centre of Browns Bay reaching the end of its useful life, Auckland Council faced a significant challenge: how to repair the pipeline without disruption to surr...
With an ageing stormwater culvert in the centre of Browns Bay reaching the end of its useful life, Auckland Council faced a significant challenge: how to repair the pipeline without disruption to surrounding residents and traffic?
With the pipe running directly under roads and properties, repairs via open-cut methods were simply not an option. Pipeworks developed a remediation strategy that saw 60 metres of the 1350mm diameter concrete culvert lined with cured-in-place-pipe, enabling the pipeline to be repaired with minimal disturbance to surrounding residents and without the need for road closures. To maintain maximum flow volumes, Pipeworks used a 33mm thick I-Plus liner to line the pipe.
Unique aspects of the project include:
The culvert followed the course of an existing stream meaning there was a constant flow of water – even in dry weather.
As the only means of access to the pipe was via a number of back sections, Pipeworks used a large crane to lift the liner in place in front of the culvert.
With no space to impregnate and invert the liner on site, Pipeworks impregnated the liner offsite and inverted it into a pre-liner. The pre-liner was then transported to site, pulled in to place and inflated – a complex and logistically challenging operation. This was the largest liner ever pulled into position in New Zealand.
Client | Auckland Council |
---|---|
Budget | $400,000 |
Completed | May 2015 |
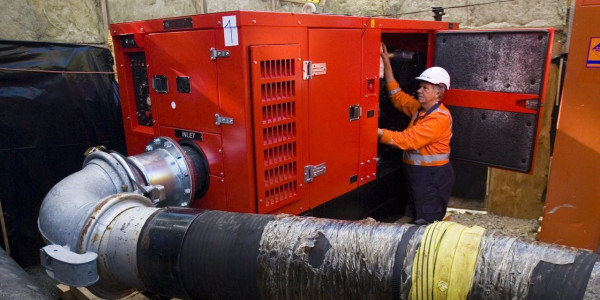

Remuera was largely farmland when the Branch 1 sewer was laid in Remuera in 1903.
Remuera was largely farmland when the Branch 1 sewer was laid in Remuera in 1903. But with the suburb now home to some of New Zealand’s most expensive properties, and the ageing sewer needing repair, trenchless rehabilitation was the only option.
Pipeworks used cured-in-place-pipe (CIPP) technology to reline a 530m long egg-shaped section of the sewer, whereby a resin-soaked ‘sock’ was installed inside the 900mm x 600mm brick and concrete structure. The resin was cured using hot water. The snug internal fit provides a permanent barrier inside the old sewer, keeping it watertight without significantly reducing the diameter and capacity of the pipe.
Pipeworks selected a thin I-Plus (fibre-reinforced) liner for the lining, as it provided the required strength with minimal reduction to the pipe’s diameter to maximise flow volume.
The heavily built-up environment added significantly to the challenge. The CIPP liners were installed 'blind' through 12m deep 900mm x 800mm chimney manholes. As these manholes were positioned in a major arterial road, significant traffic management was required.
Branch 1 is an integral component of the Auckland wastewater network, so prior to starting rehabilitation works Pipeworks installed an extensive bypass pumping system to capture all dry and wet weather flows. A section with a capacity of 250 l/s system was installed by horizontal directional drilling (HDD) under Remuera Road.
Client | Watercare Services |
---|---|
Budget | $2 million |
Completed | June 2014 |
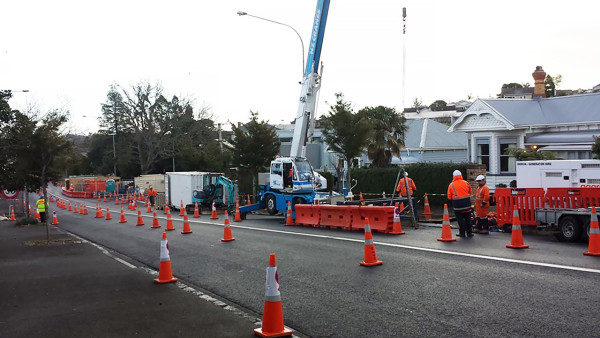

Constructed in 1910, the Orakei sewer is a critical piece of Auckland’s wastewater infrastructure, carrying sewage from Auckland’s central western suburbs to the wastewater tunnel at Hobson Bay.
Constructed in 1910, the Orakei sewer is a critical piece of Auckland’s wastewater infrastructure, carrying sewage from Auckland’s central western suburbs to the wastewater tunnel at Hobson Bay. A 250m section carries the pipeline under the Stanley Street motorway onramp, through the Auckland Domain and under the Auckland Tennis Centre. Overtime the structural integrity of the egg-shaped 2.4m x 1.5m structure had become severely compromised, requiring urgent repair.
Pipeworks developed two proposals for the relining of the pipeline: a CIPP (cured in place pipe) liner option and a glass reinforced pipe (GRP) alternative. Although the CIPP option offered significant cost advantages, the GRP option was selected because of the reduced risk profile. Pipeworks constructed a temporary pump station and rising main to enable bypass pumping of the pipeline, before relining the sewer using 25mm thick sections of GRP.
The rehabilitation works extended the life of the pipeline by 50 years.
Unique aspects of the project include:
- The project involved one of the largest and most challenging by-pass pumping operations in the country - more than 800 litres per second of raw sewage using submersible pumps.
- Construction of a 7m deep insertion pit.
- The GRP sections were installed during the wet winter season.
- Construction of an 8.5m deep pump pit to accommodate the by-pass pumps.
Client | Watercare Services |
---|---|
Budget | $5.2 million |
Completed | May 2014 |
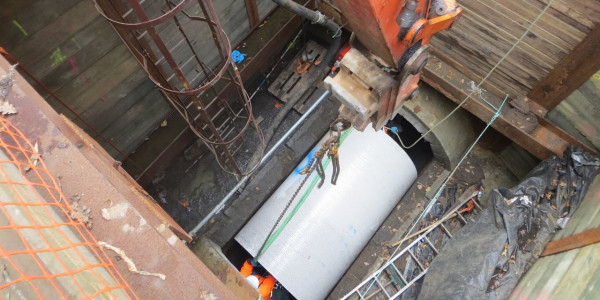

The harsh environment in wastewater treatment plants can cause significant damage to internal concrete structures over time.
The harsh environment in wastewater treatment plants can cause significant damage to internal concrete structures over time. Napier City Council engaged Pipeworks to coat and line tanks and concrete structures in its Awatoto Wastewater Treatment Plant to protect them from Hydrogen Sulphide and other corrosive gases.
Pipeworks used a two-stage rehabilitation process to protect the wet wells, effluent channels and grit channels, chambers and outlet channels. First a layer of fibreglass was glued and bonded to the existing concrete surface. Then a chemical resistant epoxy Novolac lining system was applied to provide a smooth and durable finish.
The rehabilitation works will extend the life of the wastewater treatment plant by at least 50 years.
The project had unique aspects:
- Works in wet wells and effluent channels required careful planning and special equipment due to the confined space.
- The epoxy liner and fibreglass sheets were applied from a scaffold, and entry to the chambers was via a small 800mm x 800m opening.
- Following completion of the works, the coated areas were tested using high voltage tHoliday Testing' to detect pinholes and other minor defects.
- The epoxy liner was applied in most areas with a spray gun and where a thicker application was required, a trowel was used.
Client | Napier City Council |
---|---|
Budget | $300,000 |
Completed | August 2013 |
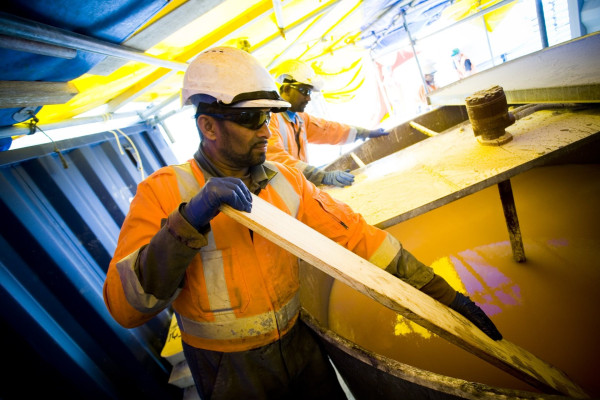

Due to being one of New Zealand’s earliest cities, many of Christchurch’s sewers were built before the invention of precast concrete pipes, using unreinforced brick and concrete.
Due to being one of New Zealand’s earliest cities, many of Christchurch’s sewers were built before the invention of precast concrete pipes, using unreinforced brick and concrete. As with brick buildings, these brick sewers are particularly vulnerable to seismic activity and some were severely damaged during the 2011 and 2012 earthquake. This highlighted the vulnerability of the infrastructure, and the need for strengthening and earthquake proofing.
Replacing the sewers would have caused major disruption to traffic and the community, so SCIRT opted to rehabilitate most of the pipelines using cured-in-place-pipe technology (CIPP).
Pipeworks relined the egg-shaped and elliptical pipes, which vary in diameter from 450mm to 1,350mm, using a very thick structural liner to protect them from future earthquakes and liquefaction. With many of the pipes running down major arterial roads, careful logistics planning and extensive traffic management was required.
All sections of CIPP liner were installed to a high standard, with minimal disruption to traffic and surrounding residents. The scale of work to be completed made this the largest CIPP project ever undertaken in New Zealand. Due to the sheer volume of work, the CIPP liners had to be installed three times faster than normal – faster than any other large diameter CIPP project in Australasia.
The project had numerous unique aspects:
- All of the pipes were more or less permanently flooded
- Bypassing of sewer flows of up to 300 litres per second – pumped above and below ground in busy streets
- Major alterations to large manholes up to 4m deep were required including well pointing and trench shields
- All resin mixing was undertaken inside the "Red Zone" to reduce risk
- Confined space entries were required to open laterals in certain pipes.
Photo courtesy of Water New Zealand
Client | Stronger Christchurch Infrastructure Rebuild Team (SCIRT) |
---|---|
Budget | $13 million |
Completed | June 2013 |
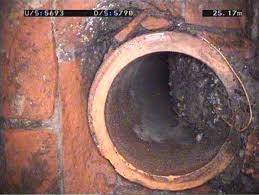

Our construction of the South Western Interceptor in 1997 saw the first use of large diameter micro-tunnelling techniques in New Zealand.
Our construction of the South Western Interceptor in 1997 saw the first use of large diameter micro-tunnelling techniques in New Zealand.
We used a tunnel boring machine to install two km of 1900mm diameter pipeline in an environmentally sensitive area adjacent to the approach path to Auckland Airport.
Fifteen years later, we extended the pipeline to Manurewa to accommodate rapid population growth in Auckland’s southern suburbs.
Due to the complex ground conditions we used three different methodologies to install the 2.3km, 900mm diameter wastewater pipe: open trenching, directional drilling and pipe jacking. A tunnel boring machine was used for the pipe-jacking section.
We also constructed a new pump station to replace the one at Manukau’s Wattle Farm Reserve, which had reached the end of its serviceable life. The pump station was constructed using in-situ reinforced concrete wet-and-dry-well internal walls and pre-cast panel roof.
The project involved significant mechanical and electrical works, including installation of four 320Kw pumps, numerous 700-900mm diameter valves, pipework, HVAC system, cooling water system and odour removal. The project team was also responsible for managing the sub-contract electrical works, which included installation of a new control system, cabling, switchboard and float switches.
The extension to the South Western Interceptor and the new pump station provided for future growth in South Auckland in as well as reducing the frequency and volume of wastewater overflows to the Manukau Harbour.
Client | Watercare Services |
---|---|
Budget | $21 million |
Completed | February 2012 |
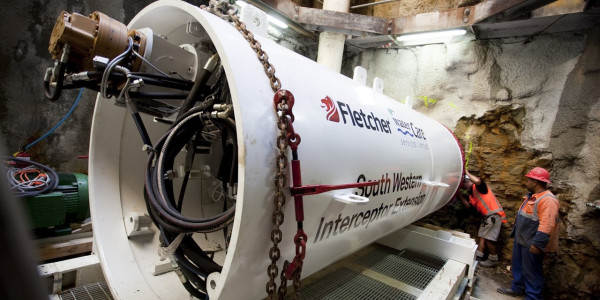

For 90 years, 25% of Auckland’s wastewater was carried via an unsightly concrete sewer pipe across Hobson Bay to the Mangere Wastewater Treatment Plant.
For 90 years, 25% of Auckland’s wastewater was carried via an unsightly concrete sewer pipe across Hobson Bay to the Mangere Wastewater Treatment Plant. As the city’s population grew, the pipeline strained to cope with demand and frequently overflowed into Hobson Bay.
We replaced the ageing pipeline with a 3km long, 3.4m diameter sewerage tunnel running 35m below sea level from Parnell to the Orakei Domain. The new tunnel provides significant additional capacity to support future growth and virtually eliminates overflows – leaving the bay open to use for swimming and boating. The tunnel connects to a new, higher capacity pump station.
The pre-cast concrete segmental-lined sewer tunnel was excavated using an earth pressure balance tunnel boring machine – the first of its scale and type in New Zealand. This allowed the tunnel to be built at a shallower depth in weaker ground conditions, thus reducing the project’s whole-of-life cost. Importantly, in the high-density urban environment, tunnelling also reduced impacts on surrounding residents.
We constructed the 22m diameter, 37m deep permanent access shaft in Orakei Domain, built new pump stations and demolished the existing pipeline, while McConnell Dowell bored the tunnel itself.
Client | Watercare Services Limited |
---|---|
Budget | $114 million |
Completed | August 2010 |




The largest environmental restoration programme ever undertaken in New Zealand, the upgrade of Watercare Services’ wastewater treatment in Mangere, reduced pathogens in the treated wastewater by 10,00...
The largest environmental restoration programme ever undertaken in New Zealand, the upgrade of Watercare Services’ wastewater treatment in Mangere, reduced pathogens in the treated wastewater by 10,000 times, raising water quality in the Manukau Harbour to its highest level since the 1930s.
The removal of the oxidation ponds not only enabled the restoration of coastal tidal flats and the rehabilitation of 13 kilometres of coastline, it also means the harbour is no longer used as part of the treatment process.
We joined forces with Civil & Civic to upgrade the existing wastewater treatment plant to meet improved discharge standards, including construction of a new advanced treatment facility, ultra-violet disinfection facilities, new biosolids facilities, upgrade of existing power supply, demolition of redundant plant, decommissioning 500Ha of oxidation ponds and foreshore restoration. The new treatment plant uses world-leading technology and has the capacity to cater for Auckland’s growing population for approximately 30 years.
Handling over 319 million litres of wastewater every day, Mangere is New Zealand’s largest wastewater treatment plant and therefore, any disruption to normal operations was simply not an option. The plant remained fully operational as the new facility was built, required a carefully staged construction and commissioning approach and astute stakeholder management.
Client | Watercare Services Ltd |
---|---|
Budget | $324 million |
Completed | December 2003 |
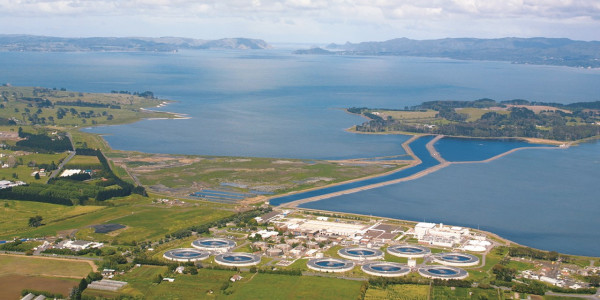